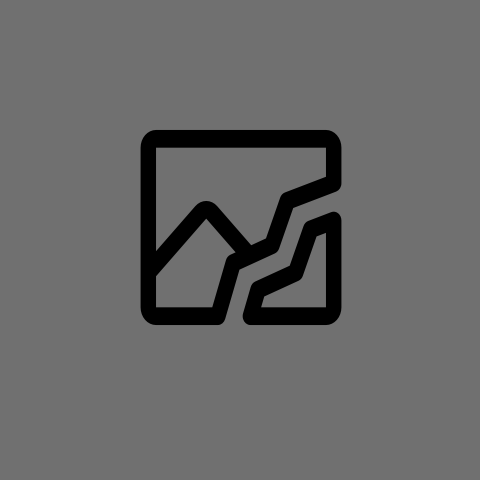
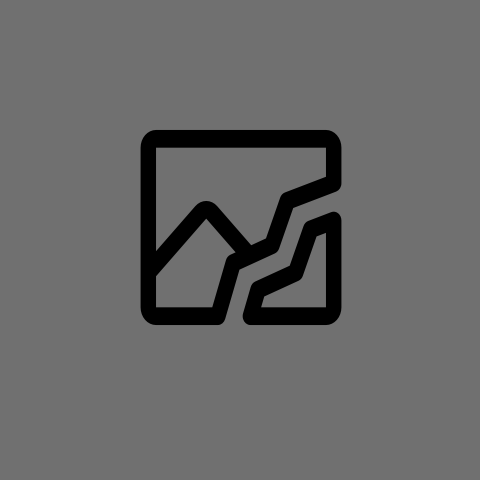
I do! But I also know that rebar tie wire is intended for static situation. This whole thing moves around quite a bit when it’s covered in leaves on a windy day
I do! But I also know that rebar tie wire is intended for static situation. This whole thing moves around quite a bit when it’s covered in leaves on a windy day
Your tuning looks great btw, look pretty nice even in the worst case lighting conditions, adhesion not an issue doing this way?
Thanks! I will make a “same print, terrible lighting vs good lighting” post in the next day or two. No, adhesion wasn’t an issue. I run klipper with z calibration, so my first layers are very consistent.
My dad asked me to print some stuff he designed for his beekeeping tools, has a bearing surface that’s awkward to print accurately, I’m probably going to resist that with this as inspiration, other than the helper ears I see on the build plate anything else you did?
Most of what I print is self designed. I do my best to make sure the designs are (reasonably) easy to print. For overhangs, printing a part at 45 degrees is basically a cheat code, but it comes with the tradeoff of more iffy bed adhesion.
I printed these with a skirt and some tree supports to improve stability. Beyond that, I didn’t do anything special and don’t put anything on my bed.
To ask questions, for the application does dimensional accuracy actually matter? AFAIK rebar isn’t exactly the tightest wrt tolerances (I know flat products, not long products, but knowing what hotroll coils look like I’m assuming it’s similar), could probably have gotten away with a different orientation and could probably have avoided supports (I find arches print nicely).
These are ASA parts with 0.3mm high layers. If you haven’t printed ASA before, it’s a bit more melty than PLA. You’re right that rebar isn’t super dimensionally consistent, but a 14mm radius cylinder wouldn’t have printed very well flat.
Having said that though, thinking strength might be another reason to print the way you did, face down and you have shear & torsion in between layers, thinking that’s still a concern if you printed it standing, but yeah, just thoughts.
I don’t think layer lines matter a ton in this particular print. Most of the stress is going to be torque caused by one bar trying to rotate relative to the other bar.
also spy kapton tape, did you find the bubble insulation made much of a difference? I’m putting what’s basically heat barrier fabric on the interior as a first try, I grabbed some rock wool and bubble insulation but it’s thick enough that I’m mildly concerned with it interfering with the gantry, having everything off for some refurb and wow I forgot just how close everything is, they really didn’t waste space eh?
A few answers here.
First, swapping to ACM panels bumped my chamber temps. If you dig through my post history you can find a temp graph comparing before/after. Second, adding a radiant barrier did help, but was less significant than the ACM panels. I do need to do the back panel and want to make my fridge door double pane using one of the stock acrylic sides. Third, I have magnetic panel clips that I modified to give me a bit more space to accommodate the radiant insulation. You would never be able to fit this stuff in with the stock panel attachments.
Happy to hear the photos revealed the mystery, lol.
Believe it or not, the outside fence, which is super jankey, is pretty effective at keeping deer out. Rabbits, not so much :(
I hope so! The zip tie solution only made it one season :(
ASA
45° is a great cheat code for overhangs assuming you can keep the parts on your bed.
It’s the center section of a rebar clamp for a plant support structure in my garden. I’m hoping to get a photo of it installed today.
First try. I’m running klipper with z calibration with a bed mesh, so my first layers are very consistent.
I manually painted the trees in two locations. The first was below the cylinder cutouts even start to give the print a touch more stability, but I probably could have gotten away without them. The second was for the small overhang at the top of the cylinder. This is ASA, which tends to sag on overhangs a bit more than PLA. A bevel would have been a great way to eliminate the need for the second set of trees.
The prints are the middle section of a rebar clamp for my garden. I’ll try to post a photo of the completed unit in a day or two. So not a jig per say, but functionally very similar. Good eye!
I updated the OP. The dimensions in the arch is the feature that matters for this print.
The prints really do look pretty good under normal lighting. The orientation did not impact print quality. Elis has a nice demo of this on his site
Only kinda sorta dangerous, I’m not leaning into chaos random. I’ll update the post with a better view of the final part. The two cylindrical recesses are the dimensionally important features and bridging would hurt that.
I ran into this at work today. Proposed a very simple approach for something to an architect and an engineering lead. Engineering lead said this was a practical solution that solves a problem that’s been plaguing them for two years. The architect nearly immediately said, “well, the real source is a mainframe that was stood up in the very early 80s. Let’s ignore the fact that changing it takes an act of Congress or that we have multiple modern downstream systems between it and us that are a much better home for this new function.”
It really seemed to amount to, “I didn’t come up with this, therefore I don’t support it.”
Ah, corporate politics.
Odds are your phone has a modern connector so this isn’t necessary. I replaced my pixel 3a, which I bought in September 2019, last December. Thanks to wired phone projection, I cycled its USB-C connector twice a day for 5 years and 3 months. That’s ~4,000 cycles. The connector specification calls for a 10,000 cycle lifetime.
I did have to de-lint the connector from time to time, but other than that I had no issues.
Not to say that you shouldn’t use inductive charging of course :)
My old i3 clone came with a 1mm steel rod I use in these situations. Leave the extruder on your printer, cut the filament off, heat up the extruder to a normal printing temp, and push the gunk through the nozzle. If you have a cold side clog you’re probably going to have to add heat from something like a heat gun.
No problem! I’m glad you were able to get to the bottom of it.
If you add position sensors to the servos you shouldn’t need much calibration after the first go, no?
It looks a lot like a typical robotic arm used in manufacturing. A quick Google shows that there are a number of desk mounted versions available, but I have no idea what kind of accuracy they offer. It shouldn’t be that complicated of a design and since most approaches use encoders things like missteps should be a thing of the past.
I can’t see pulling this off at a home user price point without pretty big compromises on positioning accuracy and/or giving up on feedback.
I would strongly suspect a retraction/priming or mechanical related issue give byhe fact that it’s repeatable in the same area of the print.
Has the printer been used recently and put out good prints? Has anything about the setup changed including a slicer update or different slicer?
I have two knee jerk reactions
Is there an under-extruded section of the print, similar to the corner closest to the camera on the lower section of the print, on the top section of the print? You might have a retraction/priming problem. A quick retraction test print would make this pretty obvious.
You might have had a partial clog that resolved itself, but the fact that the extrusion issues change with the topology of the design makes me want to suggest something else. Try the print again. If you get the same outcome filament isn’t the primary cause.
Ah, galvanic corrosion. Sealing the heat sets would be a pain as they’re open to water on both sides. I also don’t tend to take these apart, so I’m tempted to just leave them alone.